Aluminum castings play a crucial role in various industries, offering lightweight and durable components for a wide range of applications. However, the casting process often leaves behind burrs, rough edges, and imperfections that can impact the final product’s performance and aesthetics, hence a deburring process is required.
State of the art
Traditionally, this task was performed manually, but with technological advancements, automated solutions have become prevalent. The most common solution consisting of robotic deburring, systems that utilize industrial robots equipped with specialized deburring tools. These robots are programmed to perform precise movements, allowing them to reach intricate areas on a workpiece. The programming can be tailored to specific part geometries, making robots versatile for various applications.
The Lianco way
Recently Lianco has entered this arena as a new player offering CNC deburring solutions that consist of computer-controlled machining processes. Lianco deburring machines are 5 axis machining centers equipped with two position pallet changer, powerful electro spindle and optionally tool magazine designed to remove all excess material from the workpiece. This method is particularly effective thanks to the following main plus:
-
Precision and Consistency:
CNC deburring stands out for its unmatched precision and consistency. Unlike traditional robotic deburring methods, CNC machines come with high precision, ensuring that every part is treated with the same accuracy. This results in uniform finishes across a production run, eliminating variations that may arise from robot lower repeatability.
-
Increased Efficiency:
One of the key advantages of CNC deburring is its efficiency in handling large volumes of components. Automated CNC systems can process parts quickly and consistently, reducing cycle times and enhancing overall production efficiency. This is particularly beneficial in industries where time-to-market is critical and high production rates are essential.
-
Pre machining option:
CNC deburring can offer also pre-machining operation thanks to the availability of high-performance electro spindles coupled with automatic tool changer option. This combination allows the cutting / deburring / premachining of the casting in one set up reducing dramatically the manufacturing cost and time.
-
Complex Geometry Handling:
Traditional deburring methods struggle when dealing with intricate or complex geometries, leaving some areas untreated. CNC deburring, on the other hand, excels in handling complex shapes and intricate details. The programmed nature of CNC systems allows them to navigate intricate contours, ensuring that every nook and cranny is deburred effectively.
-
Cost-Effectiveness:
While the initial investment in CNC deburring equipment may seem significant, the long-term cost-effectiveness cannot be overstated. Automated processes reduce labor costs associated with manual deburring, and the consistent quality of CNC deburring minimizes the need for rework or repairs. This results in higher overall cost savings for manufacturers over time.
Conclusion
In the competitive landscape of precision manufacturing, CNC deburring of aluminum castings can be the game-changer, offering unparalleled advantages in terms of precision, efficiency, versatility, and cost-effectiveness.
It is very important for all decision makers to be fully aware of the unique potential of CNC deburring, all are welcome to meet Lianco team at next Euroguss show in Nurenberg to discover it completely.
Save the date: Euroguss – January 16th-18th, Nuremberg Germany
Hall 7A – stand 442
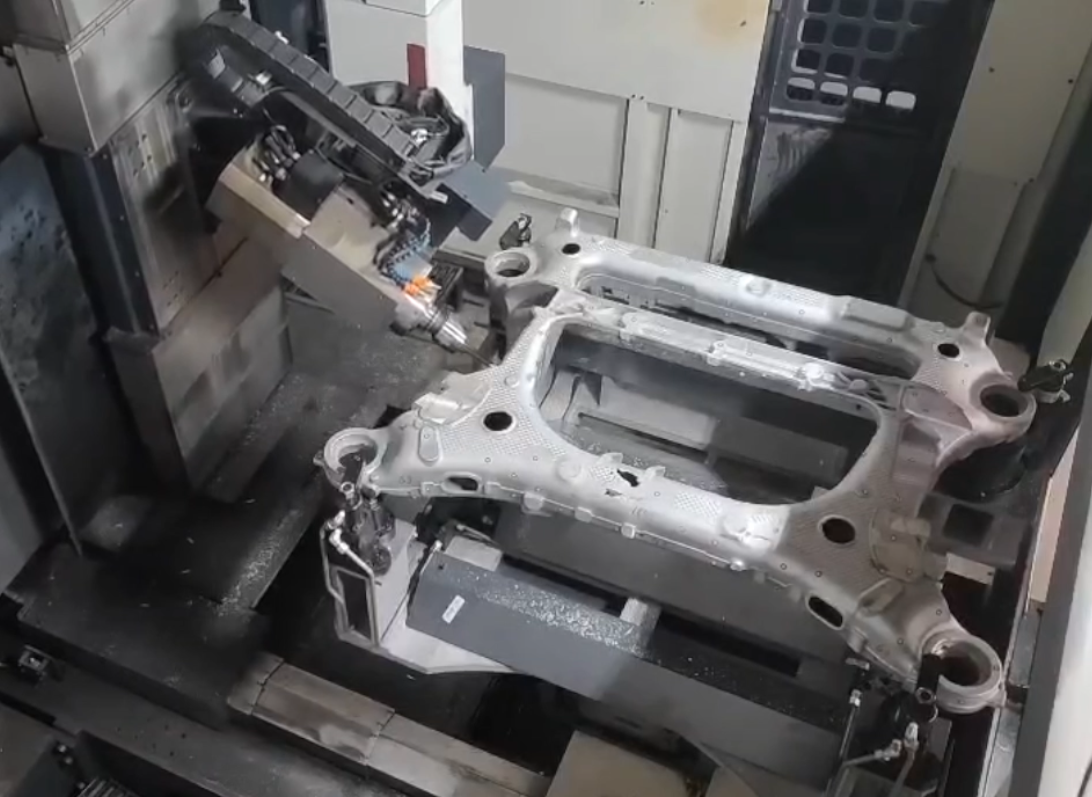